All you need to know about the spline pin
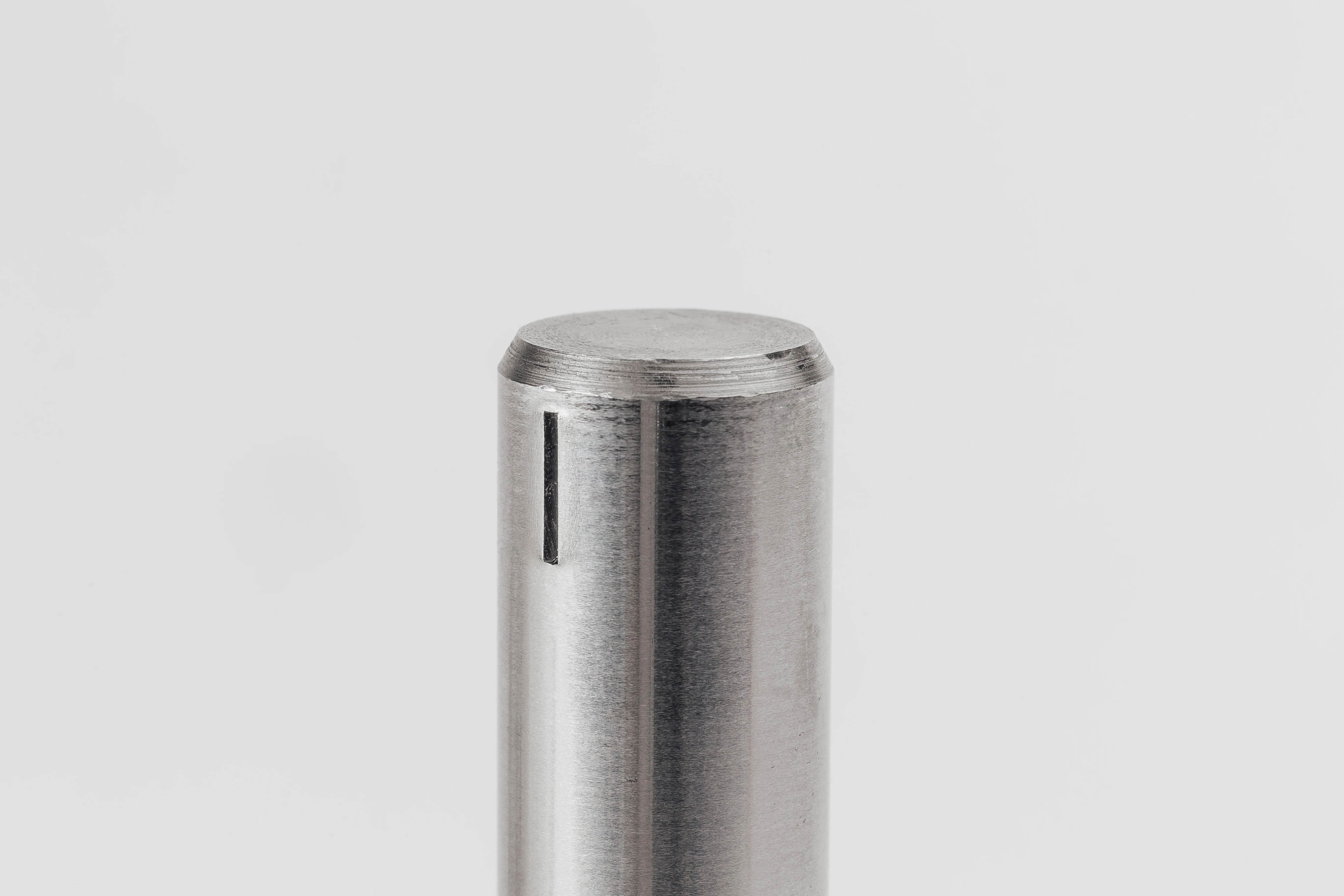
Why are there splines on some pins?
First of all, it's important to know that there are, among other things plain pins, ground pins and grooved pins.
And these parts have several functions:
- Securing one part to another: solidarization
- Positioning one part relative to another: positioning
- Acting as an axis within an assembly: rotation
- Serve as a safety component in an assembly
A splined pin can have 1, 2, 3 or 6 splines.
There are usually 3 splines at 120° for a simple reason. Forces must be distributed evenly around the assembly. The 3 splines provide isostatic support. This means that the joint operates without excessive stress, allowing forces to be transmitted throughout the assembly.
Did you know?
When there are 2 supports, it's called hypostatic support.
When there are 4 supports, it's called hyperstatic support because one support works less than the others. That's why on a 4-leg chair, there's always one leg that makes the chair unstable!
The purpose of the splines is to fit into an assembly. When the pin enters a hole, the splines partially close and the metal flows between the splines to achieve a fit between the pin and the hole. Clamping is therefore said to be elastic, rather than simply seizing.
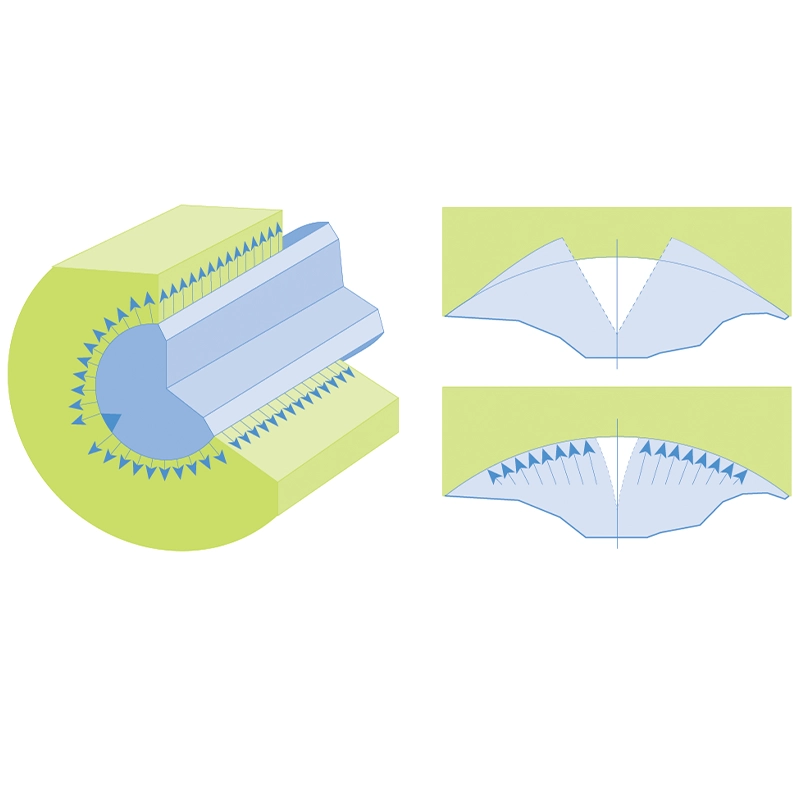
How are splined pins made?
There are several techniques and machines capable of manufacturing splined pins.
First, a specialized machine shapes the pin. This is done from an iron bar, in the desired material (stainless steel, brass, steel, aluminum, etc.):
- The bar enters the machine
- The machine cuts the bar to size
- The part is cleaned and oiled to facilitate part-machine friction
Depending on the part required, chamfers or other special features can be added using other specialized machines. The part can also undergo surface treatments if desired.
As far as splines are concerned, they are produced using a machine specially designed to LGC's specifications, which we call a "splining machine". Parts are placed in the fluting station either by hand or by robot.
When this stage is automatic, the machine picks up the part and places it in the center of the machine. Tools are then used to deform the pin with the utmost precision to form the splines. In most cases, this involves cold forming.
Did you know?
As the pin presses down on the receiver part, the diameter of the pin increases at the edge of the spline. This technical feature is called the "bulge diameter".
There are two types of tool for splining spline :
- Nails: used in "striking" bending machines. The workpiece is fixed during splining. The length of the spline depends on the width of the tool.
- Rollers: used in presses. The workpiece is fixed or in motion during the splining process. The length of the spline is variable.
What are the pin applications?
You may be surprised to find them in many of your everyday objects.
First of all, pins are used in all petrol and diesel car engines, and more recently in electric and hybrid motors, to secure various assemblies.
In cars we can also find them in :
- The gearbox
- The door
- steering column
- the fuel filler flap
- armrests
- the window mechanism
- the glove box
And more and more, pins are finding their way into electric cars: in the braking system, in battery mounting and in charging stations.
They can also be found in non-automotive applications such as non-automotive engines, removable handles and fire extinguishers.
A pin can be applied to all assemblies requiring fastening, securing or positioning.
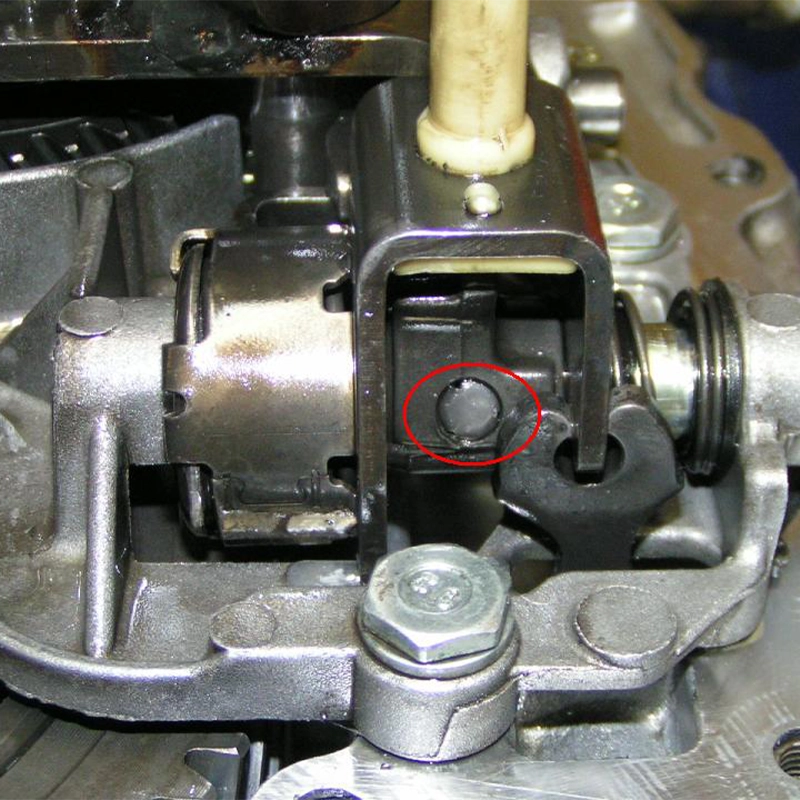
Conclusion
Grooved pins are found in many of the objects around us. If you need advice on choosing the right pins for your productions, you can turn to specialists who will help you choose the most suitable pin.
At LGC Industries, we pay particular attention to co and eco-design with our partners.
Our design office and our machine park enable us to respond to specific needs. Our multi-disciplinary team supports customers throughout the design and manufacturing process.
The in-house retrofit of of our machinery as well as the continuous improvement of our production resources will benefit from this new know-how. 3D printing and our new software facilitate the production of complex, low-stress parts and reduce heavy metal waste, in line with LGC Industries' Lean Manufacturing strategy.
To find the fastener best suited to your needs, contact us !
See you soon at LGC Industries!